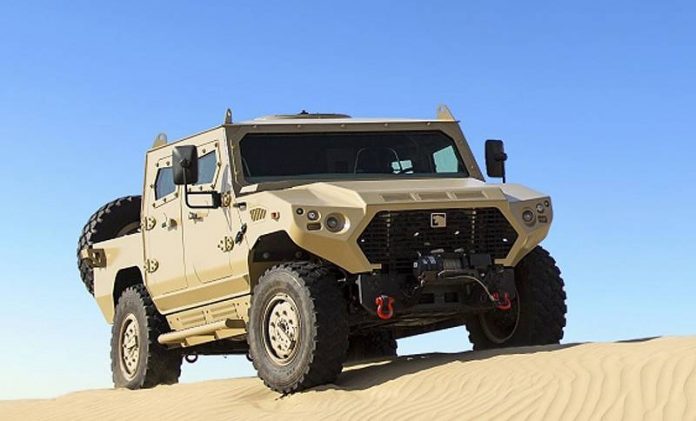
В данной статье дан обзор материалов и их сочетаний в контексте развития систем защиты.
Броня старше человечества на миллионы лет и развивалась она прежде всего для защиты от челюстей и когтей. Вполне возможно, крокодилы и черепахи могли отчасти вдохновить человека на создание элементов защиты.
Все оружие кинетической энергии, будь то доисторическая дубина или бронебойный снаряд, рассчитано на концентрацию большой силы на небольшой площади, его задача — пробить цель и нанести ей максимальный ущерб. Следовательно, работа брони состоит в том, чтобы не допустить этого за счет отклонения или разрушения атакующего средства и/или рассеивания энергии удара на как можно большей площади с целью минимизации любого ущерба живой силе, транспортным системам и сооружениям, которые она защищает.
Современная броня, как правило, состоит из твердого внешнего слоя для останова, отклонения или разрушения снаряда, промежуточного слоя, характеризующегося очень большой «работой разрушения», и вязкого внутреннего слоя для предотвращения трещин и образования осколков.
Сталь
Сталь, ставшая первым материалом, широко применявшимся при создании бронированных машин, до сих пор остается востребованной, несмотря на появление брони на основе легких сплавов алюминия и титана, керамики, композитов с полимерной матрицей, усиленных волокнами стекла, арамида и сверхвысокомолекулярного полиэтилена, а также композиционных материалов с металлической матрицей.
Многие сталелитейные заводы, в их числе и компания SSAB, продолжают разрабатывать высокопрочные стали для различного применения там, где критична масса, например, для изготовления дополнительных защитных листов.
Броневая сталь марки ARM OX 600T, доступная толщиной 4-20 мм, выпускается с гарантированный твердостью от 570 до 640 единиц HBW (аббревиатура обозначает Hardness, Brinell, Wolfram; тест, в котором вольфрамовый шарик стандартного диаметра вдавливается в образец материала с известной силой, затем измеряется диаметр образовавшегося углубления; далее эти параметры подставляются в формулу, которая позволяет получить число единиц твердости).
В компании SSAB также подчеркивают важность достижения правильного баланса твердости и ударной вязкости для обеспечения защиты от пробития и подрыва. Как и все стали, ARMOX 600T состоит из железа, углерода и ряда других легирующих компонентов, включая кремний, марганец, фосфор, серу, хром, никель, молибден и бор.
Существуют ограничения на используемые технологии производства, особенно когда речь идет о температуре. Эта сталь не предназначена для дополнительной термической обработки, при нагревании свыше 170°С после поставки компания SSAB не гарантирует сохранения ее свойств. Компании, которые смогут обойти ограничение подобного рода, скорее всего привлекут к себе пристальное внимание производителей бронетехники.
Еще одна шведская компания Deform предлагает горячештампованные детали из пулестойкой броневой стали производителям бронированных машин, в частности тем, кто занимается повышением уровня защиты машин коммерческого/гражданского происхождения.
Цельные противопожарные перегородки компании Deform устанавливаются в Nissan PATROL 4×4, микроавтобусе Volkswagen T6 TRANSPORTER, а также в пикапе Isuzu D-MAX наряду с цельным напольным листом из этого же материала. В процессе горячего формования, разработанном Deform и используемом при производстве листов, сохраняется твердость 600НВ [HBW].
В компании заявляют, что могут восстанавливать свойства всех броневых сталей на рынке и в то же время сохранять конструктивно заданную форму, при этом полученные в итоге детали намного превосходят традиционные сварные и частично перекрывающиеся конструкции. В методе, разработанном Deform, после горячей штамповки следуют закалка и отпуск листов. Благодаря этому процессу можно получать трехмерные формы, которые невозможно получить методом холодной штамповки без обязательных в таких случаях «сварных швов, нарушающих целостность в критических точках».

Стальные листы компании Deform, полученные методом горячей штамповки, используются на машинах BVS-10 и CV90 компании BAE Systems и с начала 90-х годов на многих машинах компании Kraus-Maffei Wegmann (KMW). Поступают заказы по изготовлению трехмерных броневых листов для танка LEOPARD 2 и нескольких фасонных листов для машин BOXER и PUMA плюс для нескольких машин компании Rheinmetall, включая опять же BOXER, а также люк для машины WIESEL. Компания Deform работает также с другими защитными материалами, включая алюминий, кевлар/арамид и титан.
Алюминиевый прогресс
Что касается бронетехники, то впервые алюминиевая броня была широко использована при изготовлении бронетранспортера М113, выпускающегося с 1960 года. Это был сплав, получивший обозначение 5083, содержащий 4,5% магния и в гораздо меньших количествах марганец, железо, медь, углерод, цинк, хром, титан и другие.
Хотя сплав 5083 хорошо сохраняет свою прочность после сваривания, он не относится к термообрабатывемым сплавам. У него не столь хорошая стойкость к 7,62-мм бронебойным пулям, но, как подтвердили официальные испытания, он лучше стали останавливает 14,5-мм бронебойные пули советского образца, при этом экономя массу и добавляя желаемую прочность. Для данного уровня защиты алюминиевый лист толще и в 9 раз прочнее стали при меньшей плотности 265 r/см3, следствием чего является снижение массы конструкции.
Производители бронированных машин вскоре начали запрашивать более легкую, баллистически более прочную, свариваемую и теромобрабатываемую алюминиевую броню, что привело к разработке компанией Alcan, прежде всего, сплава 7039 и затем 7017, оба с большим содержанием цинка.
Как и в случае со сталью, штамповка и последующая сборка могут негативно повлиять на защитные свойства алюминия. При сварке околошовные зоны смягчаются, но их прочность частично восстанавливается за счет упрочнения при естественном старении. Структура металла изменяется в узких зонах вблизи сварного шва, создавая большие остаточные напряжения при ошибке в сварке и/или сборке. Следовательно, технология производства должна минимизировать их, при этом риск коррозионного растрескивания под напряжением также должен быть сведен к минимуму, особенно когда расчетный срок службы машины ожидается более трех десятилетий.
Коррозионное растрескивание под напряжением представляет собой процесс появления и роста трещин в коррозионной среде, который по мере увеличения числа легирующих элементов имеет тенденцию к ухудшению. Образование трещин и их последующий рост происходит в результате диффузии водорода по границам зерен.
Определение подверженности растрескиванию начинается с извлечения небольшого количества электролита из трещин и его анализа. Испытания на коррозию под напряжением при низкой скорости деформации проводятся для того, чтобы определить, насколько сильно конкретный сплав был поражен. Происходит механическое растяжение двух образцов (один в коррозионной среде, а второй в сухом воздухе) до тех пор, пока они не разрушатся, а затем сравнивается пластическая деформация в месте разрушения — чем больше образец растягивается до разрушения, тем лучше.
Стойкость коррозионного растрескивания может быть улучшена в процессе обработки. Например, по данным справочника Total Materia, который называет себя «самой большой в мире базой данных по материалам», компания Alcan в 40 раз повысила характеристики сплава 7017 в ускоренных испытаниях на коррозионное растрескивание под напряжением. Полученные результаты позволяют также разрабатывать методы коррозионной защиты зон сварных конструкций, в которых сложно избежать остаточных напряжений.
Исследования, направленные на совершенствованию сплавов с целью оптимизации электрохимических характеристик сварных соединений, ведутся постоянно. Работы над новыми термически обрабатываемыми сплавами сосредоточены на повышении их прочности и коррозионной стойкости, в то время как работы над термически необрабатываемыми сплавами нацелены на снятие ограничений, накладываемых требованиями к свариваемости. Самые прочные материалы, находящиеся в разработке, будут на 50% прочнее самой лучшей алюминиевой брони, используемой на сегодняшний день.
Сплавы с низкой плотностью, например, алюминиево-литиевый сплав, предлагают снижение массы примерно на 10% по сравнению с прежними сплавами при сравнимой пулестойкости, хотя, согласно справочнику Total Materia, их баллистические характеристики еще должны пройти полную оценку.
Методы сварки, включая роботизированные, также совершенствуются. Среди решаемых задач — минимизация подвода тепла, более устойчивая сварочная дуга за счет совершенствования систем подачи энергии и проволоки, а также мониторинг и контроль процесса экспертными системами.
Компания MTL Advanced Materials работала с ALCOA Defense, известным производителем листов алюминиевой брони, с целью разработки, как описывает компания, «надежного и повторяемого процесса холодной штамповки». В компании отмечают, что алюминиевые сплавы, разработанные для броневых приложений, не были предназначены для холодной штамповки, то есть ее новый процесс должен помочь избежать общих режимов разрушения, включая трещинообразование.
По данным компании, конечная цель состоит в том, чтобы позволить разработчикам машин минимизировать потребность в сварке и уменьшить количество деталей. Сокращение объема сварки, подчеркивают в компании, повышает конструктивную прочность и защиту экипажа при сокращении стоимости производства. Начав с хорошо зарекомендовавшего себя сплава 5083-Н131, компания разработала процесс холодной штамповки деталей с углом изгиба 90 градусов вдоль и поперек зерен, затем перешла к более сложным материалам, например, сплавам 7017, 7020 и 7085, также добившись неплохих результатов.

Керамика и композиты
Несколько лет назад компания Morgan Advanced Materials объявила о разработке нескольких систем бронирования САМАС, которые состояли из комбинации продвинутой керамики и композиционных материалов конструкционного назначения. Линейка изделий включает навесную броню, противоосколочные подбои, капсулы живучести из конструкционных композитов для замены металлических корпусов и защиты модулей вооружения, как обитаемых, так и необитаемых. Все они могут быть адаптированы к специфическим требованиям или изготовлены по заказу.
Обеспечивается защита, соответствующая Уровням 2-6 стандарта НАТО STANAG 4569, наряду с многоударными характеристиками и снижением массы (в компании заявляют, что эти системы весят вдвое меньше в сравнении с аналогичными изделиями из стали), а также адаптация под специфические угрозы, платформы и задачи. Противоосколочные подбои могут изготавливаться из плоских панелей массой 12,3 кг для покрытия площади 0,36 м2 (около 34 кг/м2) или цельные фасонные детали массой 12,8 кг для 0,55 м2 (около 23,2 кг/м2).
По данным компании Morgan Advanced Materials, дополнительная броня, предназначенная для новых и модернизации существующих платформ, предлагает такие же возможности при вдвое меньшей массе. Патентованная система обеспечивает максимальную защиту от широкого спектра угроз, включая мало- и среднекалиберное вооружение, самодельные взрывные устройства (СВУ) и реактивные гранаты, а также многоударные характеристики.
«Полуконструкционная» система бронирования, имеющая хорошую коррозионную стойкость, предлагается для модулей вооружения (помимо воздушных и морских приложений), и наряду с экономией массы и минимизацией проблем с центром тяжести, создает в отличие от стали меньше проблем с электромагнитной совместимостью.
Защита модулей вооружения представляет собой особую проблему, поскольку они являются привлекательной целью, так как вывод их из строя резко ухудшает владение обстановкой экипажем и способность машины бороться с ближними угрозами. В них также устанавливается «нежная» оптоэлектроника и уязвимые электродвигатели. Поскольку они, как правило, устанавливаются в верхней части машины, бронирование должно быть легким с тем, чтобы удержать центр тяжести как можно ниже.
Система защиты модулей вооружения, в которую могут входить бронированное стекло и защита верхней части, является полностью разборной, два человека могут за 90 секунд собрать ее повторно. Композитные капсулы живучести изготовлены из того, что компания описывает как «уникальные прочные материалы и полимерные составы», они обеспечивают защиту от осколков и могут быть отремонтированы в полевых условиях.
Защита солдата
В систему защиты солдата SPS (Soldier Protection System) разработки компании 3М Ceradyne входят шлемы и вставки в бронежилеты для интегрированной системы защиты головы IHPS (Integrated Head Protection System) и защиты туловища VTP (Vital Torso Protection) — компоненты ESAPI (Enhanced Small Arms Protective Insert — улучшенная вставка для защиты от стрелкового оружия) системы SPS.
Требования к IHPS включают меньшую массу, пассивную защиту органов слуха и улучшенную защиту от тупых ударов. В систему также входят такие аксессуары, как компонент для защиты нижней челюсти солдата, защитный щиток-забрало, крепление для очков ночного видения, направляющие, например, для фонаря и камеры, и дополнительная модульная противопульная защита. Контрактом стоимостью более 7 млн. долларов предусматривается поставка порядка 5300 шлемов.
Тем временем, по контракту стоимостью 36 млн. будет поставлено более 30000 комплектов ESAPI — более легких вставок для бронежилетов. Производство обоих этих комплектов началась в 2017 году.
Также в рамках программы SPS компания KDH Defense выбрала материалы фирмы Honeywell SPECTRA SHIELD и GOLD SHIELD для пяти подсистем, включая подсистему защиты туловища и конечностей ТЕР (Torso and Extremity Protection), которая должна быть поставлена для проекта SPS. Система защиты ТЕР на 26% легче, что в конечном счете снижает массу системы SPS на 10%. Компания KDH в своих собственных изделиях для этой системы будет использовать материал SPECTRA SHIELD, который базируется на волокне из сверхвысокомолекулярного полиэтилена UHMWPE, и материал GOLD SHIELD на основе арамидных волокон.
Волокно SPECTRA
Компания Honeywell использует патентованный процесс формования и вытягивания полимерных волокон для встраивания исходного материала — полиэтилена UHMWPE — в волокно SPECTRA. Этот материал в 10 раз прочнее стали в пересчете на массу, удельная прочность его на 40% больше удельной прочности арамидного волокна, он имеет более высокую температуру плавления, чем стандартный полиэтилен (150°С) и большую износостойкость по сравнению с другими полимерами, например, полиэстером.
Прочный и жесткий материал SPECTRA показывает высокую деформацию при разрыве, то есть прежде чем разрушиться, он очень сильно растягивается; это свойство позволяет поглощать большое количество энергии удара. В компании Honeywell заявляют, что композиционные материалы на основе волокна SPECTRA очень хорошо ведут себя при ударном воздействии на высокой скорости, например, ударе винтовочных пуль и ударных волн.
Согласно заявлению компании, «Наше продвинутое волокно реагирует на ударное воздействие, быстро удаляя кинетическую энергию из зоны удара… оно также хорошо гасит вибрацию, имеет хорошую стойкость к многократным деформациям и отличные характеристики внутреннего трения волокон наряду с превосходной стойкостью к химическим веществам, воде и ультрафиолетовому свету».
В своей технологии SHIELD компания Honeywell раскладывает параллельные пряди волокон и связывает их вместе за счет пропитки продвинутой смолой с тем, чтобы получить однонаправленную ленту. Затем слои этой ленты размещают перекрестно под нужными углами и при заданной температуре и давлении спаивают в композитную структуру.
Для мягких приложений нательной защиты она ламинируется между двумя слоями тонкой и гибкой прозрачной пленки. Поскольку волокна остаются прямыми и параллельными, то они рассеивают энергию удара более эффективно, чем если бы были сплетены в тканое полотно.
Компания Short Bark Industries также использует материал SPECTRA SHIELD в нательной защите BCS (Ballistic Combat Shirt) для системы SPS ТЕР. Фирма Short Bark специализируется на мягкой защите, тактической одежде и аксессуарах.
По данным компании Honeywell, солдаты выбрали элементы защиты, изготовленные из этих материалов, после того как они продемонстрировали более высокие характеристики по сравнению с аналогами из арамидных волокон.
/Николай Антонов, topwar.ru/